A householder DIY Case study addressing window condensation
Dot and dab walls and aluminium double-glazed windows
Background introduction and report from the householder : –
During the first winter after moving into our new home, we experienced severe condensation issues on and around windows, particularly in occupied bedrooms. Drips of water would form on the inside face of the glass and run down onto the frame and window board leaving a film of water. There were signs of dampness in some areas around the window reveals and spots of mould were growing on the caulking between the wall and window frame. The condensation accumulated most on cold, clear nights when our days would start with mopping down the windows and frame to remove moisture.
The severity of the condensation issues came as something of a surprise to us, given that the house had double-glazed windows, albeit relatively old (installed circa 2000) and with aluminium frames. In fact, it was worse than the house we had rented previously, which had traditional single-glazed timber sash windows.
The house is a 1960s mid-terrace that required modernisation throughout (including a new heating system). We were renovating the living room and decided to do something about the windows so that condensation and damp didn’t cause us further problems. When we stripped the several old layers of wallpaper, one small section of plasterboard around the window reveal had clearly been affected by damp and was crumbling.
What we hoped to achieve
Having looked into the cost of replacement windows, and given the scale of renovation required elsewhere to the property, it was clear that we couldn’t afford to invest in new windows at this time. In any case, I was not convinced the condensation was an issue with the windows themselves but related to air leakage and “thermal bridging” around the frames – an assumption that was given some further basis when I found the Reading Draught Busters website, particularly the section on “Remedial work to window reveals in dry lined homes”.
We therefore decided to do our best to improve the existing windows by improving the insulation and sealing gaps that could result in air leakage around the frames. I “bit the bullet” and stripped the plasterboard off the window reveals using a hammer and chisel to see what we were dealing with (see below photo). At this point I contacted Reading DraughtBusters for some advice.

The photo shows plenty of gaps around the window frame where outdoor air can circulate. The cavity is “closed” with masonry, and the insulation does not meet the window frame. Both of these issues will have resulted in higher heat loss around the window frame and increased the risk of surface condensation.
Overview of Window Remedial Works Case Study
This case study details step-by-step the works undertaken to improve the thermal performance of the windows. It also covers some of the issues encountered, and how we solved them. As this was our first home, it felt a bit daunting to take on the works ourselves having limited DIY experience. However, with the support of Tony from ReadingDraught Busters, it felt achievable and has given us the confidence to tackle the other windows in the property in future.
What we did (scope of works summary):
- Removed plasterboard and bonding from the window reveals and head
- Removed window board
- Cut out section of masonry that closes the cavity
- Retrofitted insulation to cavity walls
- Installed cavity closers
- Sealed window head to lintel and filled voids with spray foam
- Installed insulated plasterboard to window opening and sealed to window frame
- Skim finish of plaster and paint
Tools and materials used are listed at each step. Specific products are mentioned in the article where they performed well for us.
Removing existing plasterboard
Having stripped the old wallpaper from the room in preparation for plastering, the first step in improving the insulation to the windows was to remove the existing plasterboard around the window head and reveals. This step revealed the construction of the window opening as well as the fixing of the window frame to the wall, and so informed the rest of the process. In our case, the cavity was closed with perforated clay blocks interleaved with half bricks. By tapping the plasterboard around the window you could identify the location of the adhesive bonding (where it sounded solid). Hollow-sounding areas (gaps in the bonding) were the best place to start working with a chisel and lever bar to pry away the plasterboard.
The below photo shows where plasterboard has been removed from one reveal and the concrete lintel has been partially exposed (there are in fact two concrete lintels placed back to back, spanning the inner and outer leaf – the absence of insulation will lead to higher heat loss).
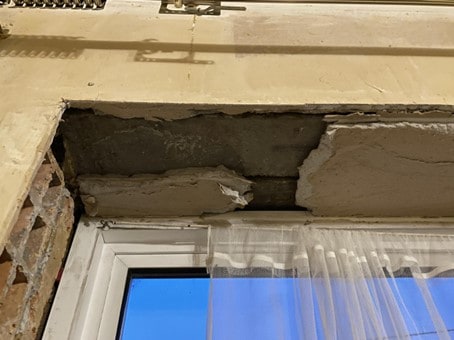
It was worth taking time at this stage to break away as much of the adhesive bonding as possible so that we would be working with a more level surface when installing the insulated plasterboard later on. Remnants of any old caulking should also be stripped away from the window frame. This step was noisy and dusty, and involved working in close proximity to the existing window with a hammer and chisel (i.e. care needs to be taken not to damage the glass, it would be sensible to protect the glazing in some way).
Tools
- Hammer
- Chisel
- Lever bar (helpful to pry away sections of plasterboard)
- Putty knife (or similar, for scraping off old caulking)
Removing the window board
The wooden window boards were fixed down with clasp headnails that were driven into the blockwork inner leaf below the window. I used a cable detector to locate the nails and then scraped away the filler to reveal the nail head. The nails were strongly embedded in the wall, so my approach here was to use a core drill around the nail head and then lift the window board up. I then cut off the nail head, which was deeply embedded in the masonry, using an angle grinder. Removing the window board revealed the cavity-fill insulation below the window. This was poorly installed mineral wool, with plenty of gaps between the batts (see photo below).

This insulation was removed and would be replaced at a later stage with new mineral wool insulation batts after cleaning the cavity.
Tools
- Cable detector
- Drill
- Core drill bits
- Angle grinder
Potential pitfalls
Work can be noisy and dusty. Proper PPE should be worn (safety glasses, gloves, ear protection), particularly when using power tools.
Real care needs to be exercised when removing plasterboard and bonding from around the window reveals using a hammer and chisel so that the glass is not accidentally damaged.
Opening the cavity
This step was probably the most daunting part of the process, but key to ensuring a continuous layer of insulation so that the window frame will stay warm in winter. As noted before, our cavity wall was closed with half bricks interleaved with perforated clay blocks. To open up the cavity would involve cutting open the section of wall as marked up by Tony below. The black line shows the clay blocks that needed to be cut. The half bricks (marked up with a red cross) are the half bricks that would then fall out.

The approach I took was to cut through the clay block with an angle grinder and then knock out any residual pieces of the block with a hammer and chisel. This was very dusty and required a steady hand to control the tool. Alternatively, a series of holes could be drilled along the line and then knocked through with a chisel, this approach being less dusty. In retrospect, I think a combination of these two approaches would have been better i.e. introducing a small number of holes using a long masonry bit (for stress relief in the clay block) and then following up with the angle grinder to achieve a neat cut as deep as it would go.
The below photos show the top part of the cavity after cutting through with an angle grinder and removing the first half brick. There is insulation behind where the brick was removed (the white fluffy stuff) that had been filled via cavity injection 20 years ago. Note also there is a dampproof membrane running from the top of the cavity along the inner face of the masonry. Beside it, the cavity wall fully opened up on one side.
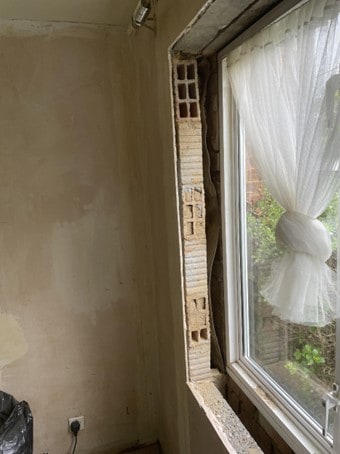

Retrofit insulation to cavity walls
It became quickly apparent that the cavity wall insulation had not achieved a full fill of insulation in this section of wall, an issue that I had not anticipated. My assumption was that insufficient injection points had been made in the wall when it was installed, or the blown insulation had been blocked by mortar “snots” within the cavity.

Given the length of time we had available to us, I decided the best thing to do was to knock down the partially filled blown insulation to create a continuous layer at the bottom of the wall and then fill up the resulting gap by pushing in mineral wool cavity insulation batts (which we had purchased for the section of wall below the window) through the reveal. This was quite a tricky procedure and I had to cut small sections of insulation and work them in carefully. It was inevitable that the insulation would be partly compressed by the installation method, but reasoned that this would be a better outcome than the alternative options (i.e. leaving the wall with gaps in insulation, or paying someone to try and reinject insulation to this section of wall). The end result is shown below, after filling the perforated clay blocks with expanding foam. Note also the gap between the plasterboard and the inner leaf has also been foamed.

Reveal ready-to-install cavity closers
My preferred approach to closing the cavity was to install a proprietary insulated closer (the grey strip of plastic in the photo below). Insulated plasterboard could just have been fixed over the gap, but I was of the view that the cavity closer would help provide a more stable backing. Also, the cavity closer was wedged between the window and the opening and then sealed with caulk, which I thought would provide a more robust air seal (I did consider proprietary airtightness tapes as well to seal to the window frame, but their cost and lack of availability at local builders merchants meant that I discounted the idea).

The cavity closer was initially secured to the inner blockwork using grab adhesive self-tapping masonry screws (note these still required a pilot hole). More of these screws were used later to mechanically fix the insulated plasterboard.
Tools/products
- Grab adhesive
- Self-tapping masonry screws
- Insulated cavity closer
- Handsaw (to cut cavity closer to size)
- Mitre block (to saw quicker and with greater control)
- Expanding foam
Sealing around the window frame
Now that the cavity closers were in, I sealed around the window reveals using acrylic caulk. This was applied in a continuous bead using a caulking gun between the window frame and cavity closer, and excess was removed using a profiling tool. The window head was a bit more tricky to insulate and make airtight.
I pushed a thin strip of mineral wool insulation through the gap between the lintel and the window frame at the top of the window. Then I squeezed in a thick wedge of foam draught stripping tape in front of the insulation, leaving a small recess between the line of the window frame and the tape. I then filled the recess with acrylic caulk (the foam draught stripping tape was essentially there to provide a stable backing for the caulk).
Installed insulated plasterboard to window opening
The next stage proceeded much quicker with some professional help. Tony kindly volunteered to help with installing the insulated plasterboard. I’d cut the insulated board roughly into shape using a plasterboard saw. The boards were then fixed to the window head using adhesive foam and applied in several continuous beads to the back of the board (i.e. the insulated side) using a foam gun as shown below.
Having pressed the first board in place by hand (it’s best to start with the window head), this was held in position using a length of wood spanning the board that was supported using an adjustable prop and a second length of wood braced against the inner leaf of blockwork below. This job really needed two props and a second pair of hands for a window of this size. The props were left in place for 24 hours.
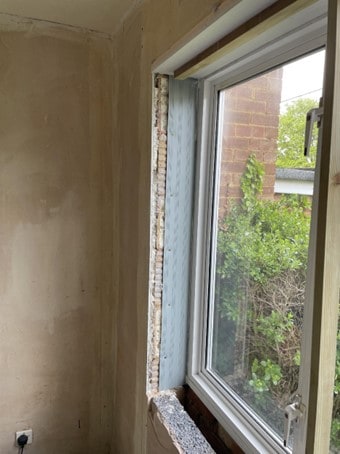
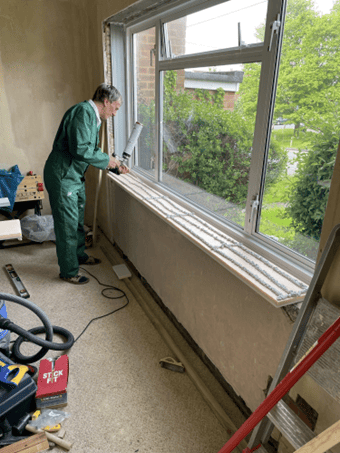
Note that just before the insulated boards were moved into place, a thick bead of acrylic caulk was applied to the edge of the window frame. The idea is that this would help create a seal between the window frame and the insulated board where the two joined. The following photo shows Tony doing this before the boards to the window reveals went on.
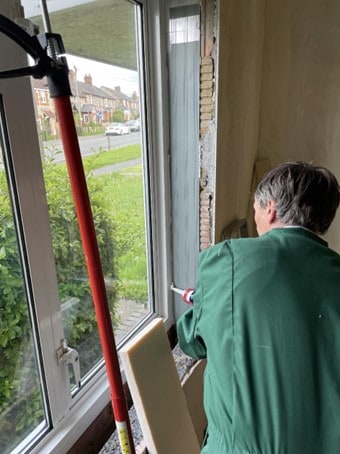
The insulated boards to the window reveals were mechanically fixed with some more self-tapping masonry screws into the clay blocks. The below photo shows three of the insulated boards in place. The boards were cut to a smooth finish to the surrounding wall using a surform, and a scrim tape was applied over the joints in preparation for plastering.
With the boards in place, another layer of caulk was applied between the insulated plasterboard and the window frame, as well as to any joints between the boards before plastering.

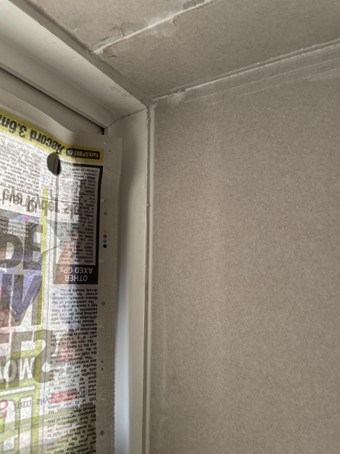
The next stage was to clear the cavity below the window and then fill with insulation batts. It wasn’t possible to fit a cavity closer across the full width below the window, as the frame was seated on the outer leaf of brickwork. However, I did manage to squeeze in a couple of short lengths of the cavity closer, thinking this would help to support the insulated plasterboard that would take the place of the original window board. Similar to other sections of insulated plasterboard, this was fixed in place with plasterboard adhesive.
Tools/Products
- Plasterboard saw
- Surform
- Stanley knife
- Adhesive foam (construction grade, suitable for fixing plasterboard) and foam gun
- Scrim tape and beading
Skim finish of plaster and paint

The final part of the work was to have the walls and ceiling skimmed. We decided to use a plasterer for this step to get a good-quality finish.
Afterthoughts
The room feels nicer, quieter and warmer. (quieter is a good indication that draughts have been sealed up DB)
Undoubtedly the work to insulate around the window frames added a lot of extra time and disruption to renovating the living room – probably equivalent to a couple of weekends extra work. We could simply have chosen to strip the wallpaper and skim over the existing plasterboard. However, this extra effort has to be weighed up against the issues that have been addressed: the improved insulation and airtightness around the window frames, as well as properly insulating the cavity wall where the original installation works were defective. If we had just (literally) skimmed over these issues, I’m certain we would have encountered the same problems as before i.e. mould growth and damage to the finishes around the windows from surface condensation, which would have been a disappointing outcome and incurred future costs to remediate. Better to do it once, and do it right. Hopefully, we will see the benefits from reduced heat loss in our heating bills, and no more troublesome condensation.